Litho vs. Screen Printing: Understanding Sign Manufacturing Techniques
For collectors of vintage advertising signs, appreciating their history and value means understanding how they were made. Two dominant printing techniques reigned supreme for decades: lithography and screen printing. While both resulted in vibrant, eye-catching signs, the methods differ significantly, impacting the sign's appearance, durability, and ultimately, its collectibility. This article delves into the technical distinctions between these processes, and provides insight for those interested in preserving pieces of Americana—like those echoes in enamel that tell stories of a bygone era.
Lithography: The Art of Stone and Oil
Lithography, derived from Greek words meaning "stone writing," was a revolutionary printing process initially developed in the late 18th century. It relies on the principle that oil and water repel each other. A smooth stone surface (originally limestone, later zinc or aluminum) was meticulously prepared. An artist would draw the design onto the stone with a greasy crayon or ink. The stone was then treated with chemicals to fix the image. The oily image accepted ink, while the surrounding areas repelled it.
When printing, the stone was dampened with water, which adhered to the non-image areas. An oily ink was then applied, sticking only to the greasy image. Paper was pressed against the stone, transferring the ink and creating the printed image.
Characteristics of Lithographed Signs:
- Fine Detail: Lithography excels at reproducing intricate details and subtle gradients. You're likely to see sharper lines and a more nuanced image compared to screen-printed signs.
- Smooth Appearance: The image tends to have a smoother, more even finish.
- Generally Thinner: Lithographed signs are often thinner and lighter than their screen-printed counterparts.
- Can Show Signs of Wear: The delicate nature of the lithographic process means these signs can be prone to scratches and loss of gloss.
The longevity and desirability of lithographed signs also depends on factors beyond the printing method itself. Collectors often seek out signs representing specific brands, particularly those with significant historical relevance. For example, a well-preserved identifying Texaco advertising signs, bearing a distinctive logo and design, can command a considerable price.
Screen Printing: A Mesh and Ink Marvel
Screen printing, also known as silk-screening, emerged as a practical alternative to lithography. It involves forcing ink through a mesh stencil supported by a frame. The stencil blocks certain areas of the mesh, allowing ink to pass through only in the desired pattern. Originally, silk was used for the mesh (hence the name), but modern screens are typically made of polyester or metal.
Each color in a screen-printed design requires a separate stencil and printing pass. This makes screen printing somewhat more labor-intensive for multi-color designs.
Characteristics of Screen-Printed Signs:
- Bold Colors: Screen printing often produces vibrant, opaque colors, even on darker backgrounds.
- Thicker Ink Layer: The ink sits on the surface of the sign, creating a noticeable texture.
- Durability: The thicker ink layer often makes screen-printed signs more resistant to scratches and fading.
- Visible Mesh Lines: Depending on the mesh used, very fine lines from the screen may be visible, especially in lighter colors or areas with very fine detail.
Beyond the technical differences, the context in which these signs were used is also key to understanding their value and cultural significance. Signs advertising sweet treats, for instance, represent a specific era of soda fountains and parlors, offering a window into the past. Exploring the signs of the soda fountain offers a charming glimpse into a different time.
Identifying the Method: A Collector’s Guide
Determining which method was used can be tricky, but here are some clues:
- Examine the Ink Layer: Feel the surface. Lithographed signs are generally smooth, while screen-printed signs will have a slightly raised ink layer.
- Look for Mesh Lines: Very fine lines may be visible on screen-printed signs.
- Consider the Detail: Intricate details and fine gradients suggest lithography. Bold colors and a thicker ink layer point to screen printing.
- Material: Early lithographed signs were often on heavier paper stock or cardboard, while screen printing could be found on a wider range of materials, including tin or aluminum.
- Color Registration: Screen-printing, when used with multiple colors, can occasionally exhibit slight misalignments or "registration errors" due to the multiple printing passes. Lithography, being a single-pass process for each stone or plate, is less prone to such imperfections.
- Edge Quality: Look at the edges of the sign. Lithography often produces clean, sharp edges, while screen printing might show a slightly rougher, more textured edge due to the way the ink is applied.
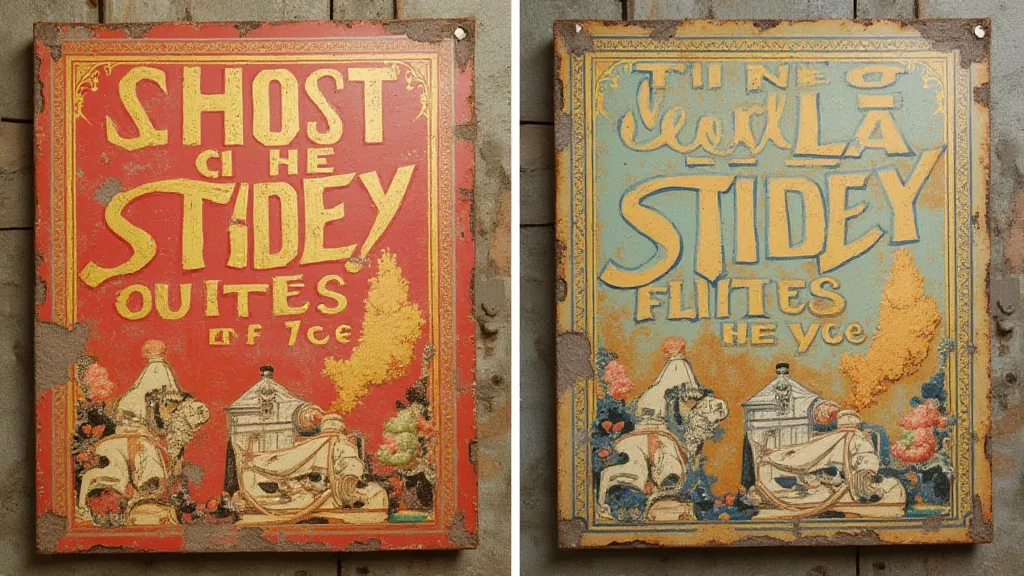
Proper storage and display are crucial for preserving these valuable pieces of history. The delicate nature of lithographed signs, in particular, requires careful handling and protection from the elements. Understanding how to protecting your sign collection, with appropriate storage and display techniques, is a vital part of ensuring their longevity and preserving their value.
A Deeper Dive: The Evolution of Printing Techniques and Their Impact on Sign Design
The shift from lithography to screen printing wasn't merely a technological upgrade; it reflected broader changes in manufacturing processes and advertising strategies. Lithography, while capable of producing incredibly detailed and artistic signs, was a relatively slow and expensive process. This made it more suitable for producing smaller runs of high-end advertising materials. Screen printing, on the other hand, offered greater speed and lower costs, enabling mass production of signs for a wider range of businesses.
This transition also influenced sign design. The limitations of lithography – the time and skill required to create a stone or plate for each design – encouraged more refined and detailed artwork. Screen printing, with its ability to reproduce bolder colors and simpler graphics, opened up new possibilities for eye-catching designs that could be mass-produced and distributed widely. The boldness and simplicity of screen-printed signs became synonymous with the burgeoning consumer culture of the mid-20th century.
Conclusion
Understanding the manufacturing processes behind vintage advertising signs enhances the appreciation for these pieces of Americana. Whether it's the delicate artistry of lithography or the bold impact of screen printing, each method contributed to the rich visual landscape of advertising history. Recognizing these differences can also inform your collecting decisions and help you accurately assess the value of your treasured signs. Ultimately, these signs aren’t just advertisements; they are tangible links to the past, offering a fascinating glimpse into a bygone era of commerce and design.